I. High-speed CNC drilling and tapping center: MK450

Product features:
-
The three-axis stroke superimposed moving column structure of the whole machine can realize the positioning and tool exchange of the three axes, the main axis and the additional axis while the worktable is rotating. It saves the time of changing the working table, realizes no-stop processing, and improves the processing time efficiency.
Application area:
-
aluminum processing, precision molds, precision parts processing.
Design features:
1. Rotary table device: using the latest direct-drive motor transmission mechanism, the transmission speed is fast, and the maximum table exchange time is only 1.5S
Product features:
-
The three-axis stroke superimposed moving column structure of the whole machine can realize the positioning and tool exchange of the three axes, the main axis and the additional axis while the worktable is rotating. It saves the time of changing the working table, realizes no-stop processing, and improves the processing time efficiency.
Application area:
-
aluminum processing, precision molds, precision parts processing.
Design features:
1. Rotary table device: using the latest direct-drive motor transmission mechanism, the transmission speed is fast, and the maximum table exchange time is only 1.5S
2. No-stop processing: high-speed non-floating table exchange and sealed structure achieve high reliability. If one working table is in the process of processing a part, the other working table can be used to replace the work piece that saves time in pieces’ replacement and allows the machine to achieve non-stop processing. It shortens the ineffective processing time and improves processing efficiency.
3. Wide clamp area: The standard turning diameter is 1100mm, the clamp height is 320mm, and the maximum load on one side is 120kg. The larger clamping area makes it easier to place a work piece on the dividing device and secure it.
Technical features
1. Direct drive to spindle:
sensitive response, full power operation, no power loss or noise like belt drive. Rigid threading does not cause problems with transmission backlash. Centralized lubrication system: the lubrication system uses volumetric (quantitative) centralized lubrication method to ensure that each lubrication point is regularly supplied with the required amount of lubricant, making the lubrication process more smart and balanced, reducing friction losses and saving lubricating oil consumption.
2. FANUC servo system:
The configuration is comprehensively improved to achieve the high performance of the FANUC system. The system uses the latest 0i Mate-MD 5-pack system, with AICCI + interpolation front bell-shaped acceleration and deceleration + processing condition selection function. The system is built on the work piece processing performance and meets the needs of most users. The servo system features an integrated higher power drive using an αis feed motor and an improved αiI spindle motor to achieve optimal drilling and tapping performance. The mainspindle motor runs at max.2 0,000 rpm, making it unique among other offers on the market.
The main parameters
Specifications
Unit
MK450
Working table size
600-840
mm
T-shaped slot specification
mm
X axis-3-T14H8
Working table max. load/ uniform load
120/200
kg
X/Y/Z axis stroke
mm
450 / 320 /320
Distance from spindle nose to table surface
mm
200-520
Distance from spindle center to column
mm
465
Mainspindle speed
rpm
20000
Mainspindle taper
BT30
X/Y/Z-axis fast movement speed
mm/min
48000 Direct coupling
Cut speed
mm/min
1-10000
Positioning accuracy
0.008
mm
Repeatability of positioning accuracy
mm
X\Y\Z: 0.005
Tool magazine capacity
т
20
Maximum cutting tool diameter / length / weight
80/250/30
Tool exchange time (T-T)
s
2
System
FANUC 0i-MF
Machine weight
kg
4000
Machine sizes (length × width × height)
mm
1600 ×2800× 2300

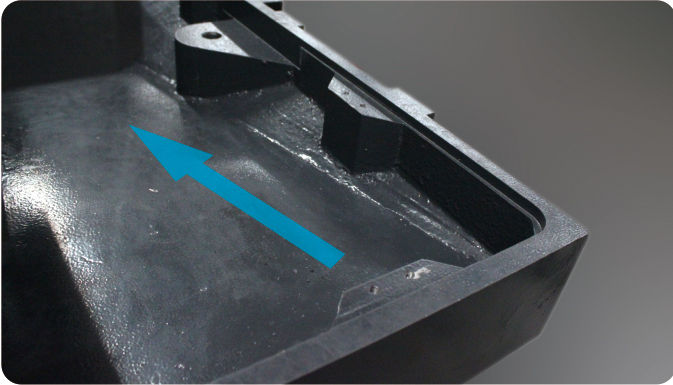

The magazine is a revolver type, the time to replace one tool with an adjacent tool is 1.8 s. The 16-tool magazine has a new tool changer turret design. The rotation of the tool magazine is forced by a spindle, that provide fast and accurate tool changes.
Metal sheet built-in leak-proof framework is designed to flash chips and throw chips out in the backward direction.
The machine bed chip throwing system makes chips throw out in the backward direction, providing a suitable chip throwing angle.
Heavy-duty roller guides are used to move along three axes.
To move along three axes, heavy-duty roller guides with a higher load-bearing capacity are used.


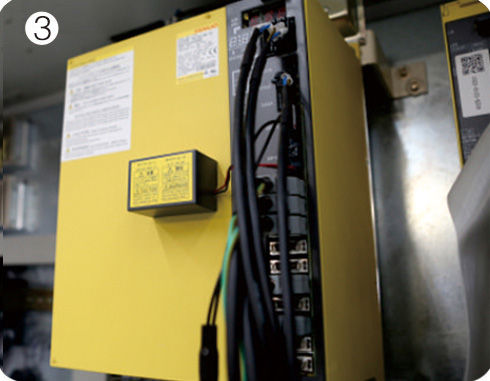


